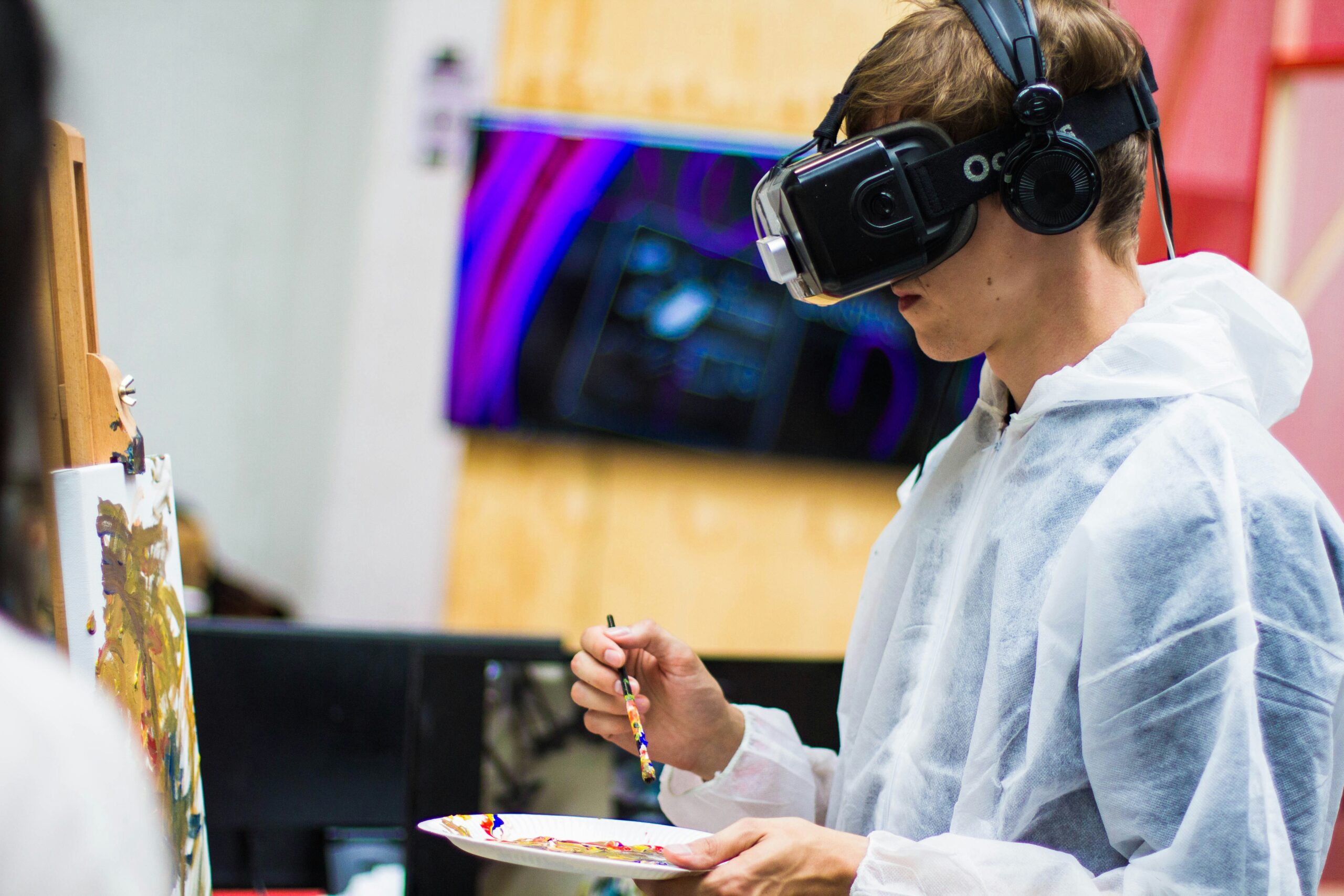
The manufacturing industry is transforming as never before. Advanced Technologies are pushing the boundaries of what’s possible, leading to faster, more efficient, and cost-effective production methods. From artificial intelligence (AI) and robotics to additive manufacturing and the Internet of Things (IoT), these innovations are revolutionizing production processes. As manufacturers embrace these cutting-edge technologies, they are not only improving productivity but also creating a new era of precision and sustainability. Let’s explore how these technologies are reshaping the manufacturing landscape.
Automation: The Heart of Modern Manufacturing
Automation has been a game-changer in manufacturing. The rise of industrial robots and automated systems has streamlined production, reducing the need for human intervention in repetitive tasks. Robotics once limited to a few tasks, now performs a wide range of operations, including assembly, welding, packaging, and inspection.
AI-powered robots are capable of learning from their environment and making real-time adjustments to improve efficiency. These robots are increasingly being used in collaboration with humans, leading to a rise in “cobots” (collaborative robots). Cobots work alongside human workers, handling dangerous or monotonous tasks while allowing humans to focus on higher-value activities. This synergy between humans and machines has resulted in higher productivity and fewer errors.
Moreover, automation doesn’t only improve production speed; it also enhances safety. Automated machines can perform hazardous tasks, keeping workers out of harm’s way. The integration of AI in automation also helps identify problems in production lines before they lead to costly delays, improving overall efficiency.
Additive Manufacturing: A New Era of Customization
Additive manufacturing, or 3D printing, has brought a revolutionary shift in how products are designed and produced. Unlike traditional manufacturing methods, which involve subtracting material from a larger piece, 3D printing builds objects layer by layer. This method allows for highly complex designs that would be impossible or too expensive to create using conventional techniques.
One of the biggest advantages of 3D printing is its ability to produce customized products. Manufacturers can create tailored solutions to meet the specific needs of customers, whether it’s for individual components or entire products. This is particularly beneficial in industries like aerospace, automotive, and healthcare, where customization is often critical.
3D printing also helps reduce waste and lower production costs. Since it only uses the exact amount of material needed for each part, the material waste is minimal. Furthermore, it accelerates prototyping, allowing engineers to quickly test and modify designs before moving to mass production. This speeds up the product development cycle and cuts down on costly errors.
Artificial Intelligence and Machine Learning: The Brain Behind Smart Manufacturing
Artificial Intelligence (AI) and Machine Learning (ML) are among the most significant forces driving innovation in manufacturing. These technologies enable machines to analyze large amounts of data, make decisions, and learn from experience, mimicking human intelligence. AI-powered systems can optimize production schedules, predict equipment failures, and identify inefficiencies in the supply chain.
In predictive maintenance, AI and ML are used to monitor machinery in real time, identifying issues before they lead to breakdowns. By analyzing data from sensors and historical performance, AI can predict when a machine will need maintenance, reducing downtime and avoiding costly repairs.
Machine learning is also used in quality control. By analyzing product data, AI can detect defects that may go unnoticed by human inspectors. This improves the overall quality of the products and reduces waste.
Moreover, AI enhances decision-making. It can process massive amounts of data from various sources, including sensors, social media, and customer feedback. This data-driven approach allows manufacturers to make more informed decisions, improving their products and services.
The Internet of Things (IoT): Connecting the Factory Floor
The Internet of Things (IoT) has created a connected world where machines, devices, and systems communicate with each other in real time. In manufacturing, IoT is a game-changer, enabling smart factories that can monitor and optimize production processes.
IoT devices, such as sensors and smart machines, collect data throughout the production process. This data is sent to centralized systems, where it can be analyzed to improve operational efficiency. For example, IoT sensors on machinery can monitor temperature, vibration, and wear-and-tear, providing manufacturers with real-time insights into the health of their equipment.
By connecting machines to the internet, manufacturers can remotely monitor and control their production lines. This improves efficiency, reduces maintenance costs, and ensures that production runs smoothly without interruptions.
IoT also plays a crucial role in supply chain management. With real-time tracking, manufacturers can monitor inventory levels, track shipments, and ensure that raw materials are always available. This leads to better inventory management and fewer delays in production.
Sustainability in Manufacturing: Green Technologies for the Future
As the world increasingly focuses on sustainability, the manufacturing industry is finding ways to reduce its environmental impact. Advanced technologies are enabling manufacturers to adopt greener practices, reducing energy consumption, waste, and carbon emissions.
One key area is energy efficiency. Technologies such as smart grids, energy storage systems, and energy-efficient machines are helping manufacturers cut down on their energy use. Smart grids, for example, can help factories optimize their energy consumption by using real-time data to adjust power usage based on demand.
Additionally, additive manufacturing plays a role in sustainability. By using only the necessary amount of material, 3D printing minimizes waste and reduces the environmental impact of production. Moreover, manufacturers are increasingly using sustainable materials, such as biodegradable plastics and recycled metals, in their production processes.
The focus on sustainability is not limited to reducing waste. It also extends to the lifecycle of products. With advanced technologies, manufacturers can create products that are easier to recycle, reducing the amount of waste that ends up in landfills. Moreover, by using AI and IoT, manufacturers can optimize their processes to ensure that they are operating in the most energy-efficient and environmentally friendly manner possible.
The future of manufacturing is undoubtedly tied to the adoption of advanced technologies. From automation and AI to 3D printing and IoT, these innovations are transforming production processes, making them faster, more efficient, and more sustainable. As manufacturers embrace these technologies, they are not only enhancing their bottom line but also setting the stage for a more connected, intelligent, and environmentally conscious industry.
The revolution in manufacturing is still in its early stages, and we can expect even more breakthroughs in the coming years. As these technologies continue to evolve, they will reshape the way products are made, paving the way for smarter, more flexible production systems that can meet the demands of an ever-changing world. The possibilities are endless, and the future of manufacturing looks brighter than ever.