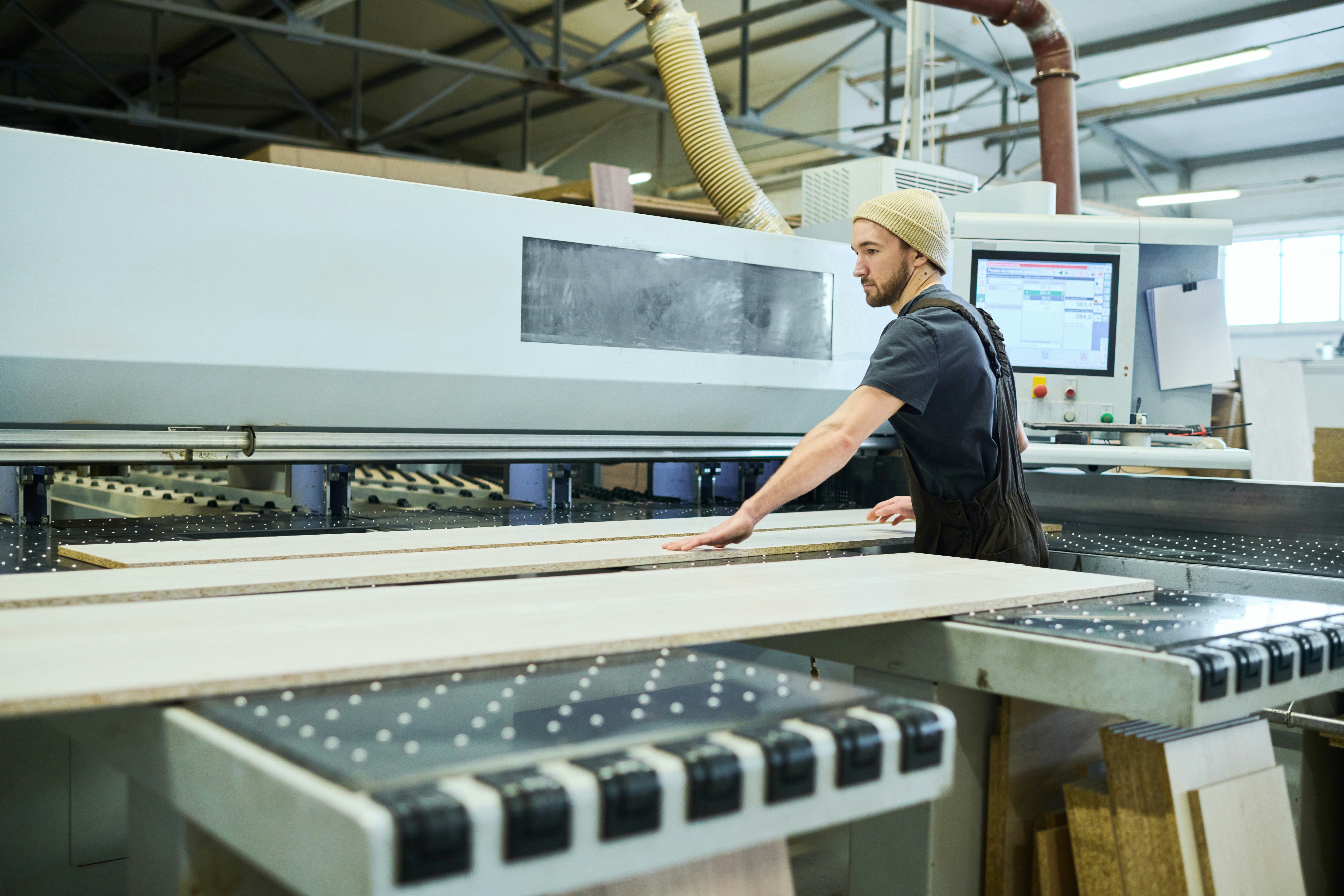
As the global focus on environmental responsibility grows, industries reevaluate their practices to become more sustainable. Manufacturing, being a major contributor to environmental degradation, is no exception. With increasing pressure from consumers, governments, and environmental organizations, modern manufacturing must adapt to more sustainable practices to ensure long-term viability and reduce its ecological footprint. Sustainability in manufacturing is not only about lowering environmental harm but also about creating economically viable and socially responsible processes. This approach has become integral to business operations and success.
Reducing Waste in Manufacturing
One of the most effective ways to make manufacturing more sustainable is to reduce waste. Waste reduction involves reducing excess materials, energy consumption, and non-recyclable products throughout the production cycle. Manufacturers can reduce their environmental impact by improving waste management and production efficiency, and simultaneously cutting costs.
To reduce waste, manufacturers can adopt practices like Lean manufacturing, which focuses on eliminating waste through continuous improvement and process optimization. Additionally, advanced technologies like automation and artificial intelligence (AI) can help streamline processes, minimizing unnecessary material use and energy waste. For instance, AI-powered predictive maintenance can prevent equipment failure, thus avoiding production delays and material waste. By addressing waste at every production stage, manufacturers contribute to a healthier planet and improve their bottom lines.
Energy Efficiency in Production
Energy consumption is one of the most significant contributors to environmental impact in manufacturing. Manufacturers must prioritize energy efficiency to reduce their carbon footprint and operational costs to operate sustainably. One way to achieve this is through using renewable energy sources, such as solar, wind, or geothermal power, which can replace traditional fossil fuels and decrease reliance on non-renewable resources.
Furthermore, manufacturers can implement energy-efficient practices within their facilities. For example, using energy-efficient machinery, better insulation, and optimized production schedules can help reduce overall energy consumption. In doing so, manufacturers can lower operational costs and reduce their contribution to climate change.
Sustainable Materials and Resource Management
Another critical aspect of sustainable manufacturing is the use of sustainable materials. Traditionally, the manufacturing industry has relied heavily on finite natural resources, leading to over-extraction and environmental harm. However, with the growing demand for sustainable practices, manufacturers are increasingly seeking alternative, environmentally friendly, and durable materials.
Furthermore, manufacturers are focusing on improving their resource management by reducing water consumption, using less toxic chemicals, and minimizing the depletion of natural resources. By sourcing sustainable materials and implementing efficient resource management practices, manufacturers contribute to the circular economy and reduce their environmental impact.
Design for Sustainability
Sustainability in manufacturing doesn’t just happen during the production process; it also starts at the design phase. By adopting design for sustainability (DFS) principles, manufacturers can create products that are easier to recycle, have a longer lifespan, and consume fewer resources. This approach encourages designers to think beyond the initial product development and consider the entire lifecycle of a product, from its creation to its eventual disposal.
Incorporating sustainability into the design phase can involve using biodegradable materials, reducing the number of components to simplify recycling, or creating modular products that can be easily repaired or upgraded. A prime example is the growing trend in the electronics industry, where manufacturers design products with replaceable parts, making them more sustainable and extending their usable life.
Additionally, manufacturers can lower energy consumption during production and transportation emissions by optimizing product design for energy efficiency or reducing weight. Adopting sustainable design practices minimizes environmental impact from the beginning of a product’s lifecycle.
Circular Economy and Product Life Cycle
The concept of a circular economy is gaining traction in the manufacturing sector as a way to promote sustainability. Unlike the traditional linear economy, where products are made, used, and disposed of, the circular economy continually uses resources by designing products with their entire life cycle in mind. In a circular model, products are designed to be reused, repaired, or recycled, reducing waste and conserving valuable resources.
Manufacturers embracing a circular economy approach are increasingly investing in recycling programs and taking back used products to repurpose materials or refurbish goods for resale. This helps reduce landfill waste and creates a more sustainable business model by maintaining the value of resources. For example, the automotive industry has been shifting towards creating easier vehicles to disassemble and recycle parts. Companies are also exploring options for creating a product-as-a-service model, where customers lease products instead of purchasing them outright, thus encouraging return and reuse. By integrating circular economy principles into their business model, manufacturers can reduce waste, conserve resources, and lower costs, all while promoting environmental stewardship.
Collaboration and Industry Standards
Sustainability in manufacturing is not just the responsibility of individual companies; it also requires collaboration within the industry. Manufacturers are increasingly working together, sharing best practices, and adhering to industry-wide sustainability standards to make a collective impact. For instance, global initiatives such as the United Nations Global Compact and the ISO 14001 Environmental Management Standard have created frameworks encouraging manufacturers to adopt sustainable practices and measure their environmental performance.
Additionally, supply chain collaboration is vital to ensuring sustainability. Manufacturers must work with suppliers and partners to ensure that sustainability is embedded throughout the entire production process. This could involve sourcing raw materials from certified sustainable sources, ensuring fair labor practices, or sharing resources to reduce energy consumption. By working together and aligning with industry standards, manufacturers can scale their sustainability efforts and create a broader, more significant impact on the environment.
Sustainable practices in modern manufacturing are essential for ensuring the industry’s and the planet’s future. Manufacturers can significantly reduce their environmental footprint while remaining competitive and profitable by focusing on waste reduction, energy efficiency, sustainable materials, and circular economy principles. Furthermore, adopting sustainable practices leads to innovation, improved resource management, and a more engaged workforce. As consumers and regulatory bodies demand greater environmental responsibility, manufacturers embracing sustainability will help protect the planet and be better positioned for long-term success. Transitioning to sustainable practices is not just a trend—it is the future of manufacturing.